Garment Storage & Retrieval Systems
Automated Uniform Storage & Retrieval Conveyor Systems
Hi-tech conveyor systems for uniform rooms in hotels, resorts & casinos.
SWIPE YOUR ID CARD, WAIT 12 SECONDS, THE DOOR OPENS AND YOUR UNIFORM IS THERE READY TO GO.
A fully staffed wardrobe with a service counter is rarely efficient – staffing levels are set to meet peaks in demand and as a consequence, the counter staff are not busy between shifts. While they have other duties, these become inefficient due to the constant demand for counter service.
Even though demand for uniforms on the 2 night shifts is light the wardrobe still has to be manned.
Over 20 staff can get their uniforms at the same time, the average waiting time is approximately 12 seconds. The carousel takes the shortest route, is 100% accurate, and is easy and safe to use.
There is a far better way -
THE HIEMAC ELECTRONIC WARDROBE
- Handle peak change over periods with ease and eliminate staff waiting times.
- Reduce wardrobe operating costs – because staff take out and put back their own uniforms 24 hours a day any time they want.
- Labor savings of over 80% when compared to a conventional manned counter. This modern system gives you maximum efficiency with minimum wardrobe staff.
- Your wardrobe could only need to be manned during the day shift letting staff get their own uniforms from the self serve door over the next two shifts.
- Move, process and store more uniforms with less operators and less effort. No lifting and carrying of garments, everything is moved easily on Hiemac’s ‘Speed Rail’.
- Reduce floor space – the Hiemac carousel system and ‘Electronic Wardrobe’ is the most compact and efficient installation available.
- Keep control of your uniforms, know where they are and reduce losses with the RFID uniform and linen inventory management software.
The automatic sliding door takes up no room in the passageway and the select and separate mechanism makes it easy to select the garments you require for the day.
A change of shift is easily executed without a wardrobe attendant being involved. The Hiemac ‘Electronic Wardrobe’ drastically reduces staff waiting times and gives them automatic access to their uniforms 24 hours a day. The average waiting time is approximately 12 seconds and over 26 staff can get their uniforms at the same time.
The ‘Electronic Wardrobe’ is a fully automated, computer controlled, garment storage and retrieval carousel system.
There is generally several carousels in a bank with one end of each carousel attached to an automatic door. The staff member swipes their ID card through a card reader, instantly the carousel calculates the shortest route and brings that staff members uniform to the door.
The ‘select and separate’ mechanism separates the staff members uniform from the others while the door is opening, they then select the required garments and go off to the change room. The door will close automatically.
Freshly laundered garments are put away onto the rear of the carousels during the quieter times of the day directly from over head speed rail trolleys. When staff are getting their uniform from the ‘Electronic Wardrobe’ door, the attendant loads the next adjacent carousel.
At the end of the shift, if their locker is small, they return to the auto door and put some of their uniform back on the carousel and throw the soiled garments through the laundry return window on the way out of the building.
Video – Hiemac Electronic Wardrobe
At the change of each shift the staff put their own uniforms back on the carousel and throw their soiled garments through the appropriate window directly into the laundry bag on the other side. The RFID tags on the garments are automatically read as they pass through the window.
The Hiemac Carousel showing the sturdy, well engineered construction with the fully sealed German gear motor and variable speed drive controller.
The patented Hiemac ‘select and separate’ system is quick and 100% accurate. It locates the staff members garments, locks out the garments on either side and separates and spreads the garments making it easy for the staff member to select the garments they want.
The successful Hiemac Carousel is the result of many years of development based on hands on experience and good planning.
They are smooth, quiet and fast with variable speed and variable acceleration. The extruded aluminium track fully encloses the chain wheels eliminating dirt falling on to the garments below, there are no exposed drive components, no dangerous nip points and there are precision, sealed ball bearings in the chain wheels.
These carousels will not need servicing or repairs for many years. We have 22 carousels at Crown Casino Melbourne, they have been running heavily loaded, 24 hours a day, 7 days a week for over 16 years.
‘Electronic Wardrobe’ can be controlled by our stand alone computer system ‘Smart Swipe’.
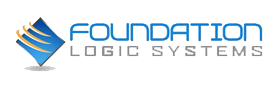
RFID UNIFORM MANAGER
Uniform Manager is built on the Microsoft.net platform and incorporates the latest RFID tag and reader technology to deliver a robust yet simple solution to manage your day to day uniform operations. Uniform Manager shares information by establishing a centralised data management system creating real-time connections between the uniform room and the laundry.
Working with management our staff builds a customised database incorporating all property areas and departments. Items entered into the system with a unique RFID tag contains the description, the manufacturer item number, the acquisition cost and date. The exact status and location of every asset is known and monitored in the system.
Uniform Managers primary objective is to provide a uniform management system that delivers significant savings and benefits by managing uniform allocation and tracking.
It achieves this by -
- Maintaining par levels of inventory while reducing purchasing.
- Analysing and improving uniform processes and productivity.
- Improving decision making through extensive reporting capabilities.
- Eliminates manual inventory time, hundreds of garments can be scanned instantly at one time.
RFID identification tags are sewn into the garments at strategic places for automatic scanning.
SAVE TIME, REDUCE YOUR STAFF LEVELS, KEEP TRACK OF YOUR ASSETS, REDUCE SHIFT TURNAROUND TIMES AND KEEP YOUR COSTS DOWN.
MAKE A SMALL INVESTMENT IN -
THE HIEMAC ELECTRONIC WARDROBE
(THE RETURN ON INVESTMENT CAN BE LESS THAN ONE YEAR)
400 uniforms move along the speed rail from the loading dock, across the passage way into the uniform distribution centre. All the RFID tags on the uniforms are automatically read as they pass through the doorway. On completion of the delivery and pick up process the speed rails fold up into the ceiling area.
The ‘Electronic Wardrobe’ is only part of the Hiemac uniform distribution centre, every thing is moved around on ‘Speed Rail’, an over head rail system carrying frictionless, 1m long, speed rail trolleys. No lifting, no carrying, the smallest operator can move 500kg of garments along the rail with ease.
Clean uniforms are delivered directly from the laundry hung on speed rail trolleys. Soiled garments are taken back to the laundry in 80kg laundry bags on the return trip on the same trolley. Every thing rolls on and rolls off.
Our ‘Rapid Load’ system enables uniform deliveries to be rolled into a lift, taken up several floors and rolled out into the uniform distribution centre.
The whole system is quick and slick, saves loads of time and does not take up any floor space.
Speed rail can be used exclusively throughout the wardrobe area as it leaves the floor uncluttered and safe, the trolleys move easily from place to place and are ideal to work from. Productivity is achieved with ergonomically designed work stations and good material flow through the uniform distribution centre.
Our adjustable uniform racking is ideal for storage for stock service and seasonal stock.